Konstruktion von Traktionsbatterien für schwere Nutz- und Industriefahrzeuge
Wie wählen wir eine Traktionsbatterie für unser zukünftiges Hybrid- oder Elektrofahrzeug aus? Welche Technologie wird am besten geeignet sein? Wie kann man sich in der Fülle von Technologien und Anbietern zurechtfinden?
Man kann sagen, dass die Konstruktion eines Elektro- oder Hybridfahrzeugs mit der Batterie beginnt und endet. Die Art der Traktionsbatterie bestimmt den Betriebsrhythmus des Fahrzeugs, vor allem wegen ihrer Ladegeschwindigkeit und ihrer Lebensdauer.
In letzter Zeit werden hauptsächlich Lithiumbatterien für die Traktion verwendet. Für einige Anwendungen kommen immer noch Blei- und Nickelbatterien zum Einsatz. Doch das ist eher eine historisch bedingte Abweichung bei Anwendungen, die noch nicht umgerüstet wurden und bei denen das hohe Gewicht keine Rolle spielt.
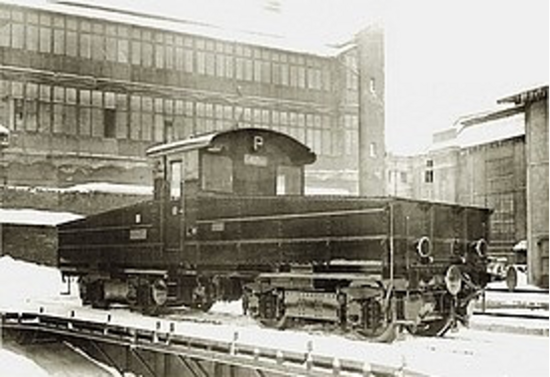
Entwicklung
Die Entwicklung von Blei-Säure- und Ni-Cd-Batterien begann im 19. Jahrhundert und so auch die ersten Versuche mit batteriebetriebenen Fahrzeugen. Im kommerziellen Betrieb wurden sie beispielsweise für Lastwagen oder Rangierlokomotiven eingesetzt. Im Jahr 1926 wurde die batteriebetriebene Rangierlokomotive E 407.0 von den Firmen František Křižík und ČKD (elektrischer Teil – elektrische Ausrüstung) und Breitfeld & Daněk (mechanischer Teil – Fahrgestell) hergestellt. Zum Zeitpunkt ihrer Herstellung war sie die größte Batterielokomotive der Welt. 440 V mit einer Kapazität von 392 Ah (172 kWh) bei einstündiger Entladung und einer Kapazität von 630 Ah (277 kWh) bei fünfstündiger Entladung) [1].
Die Entwicklung von Lithiumbatterien begann in den 1980er Jahren, und heute können wir sagen, dass wir uns in der Zeit ihres bisher größten Booms befinden.
Gängige elektrische und hybride Anwendungen von heute
- Flurförderzeuge, die in Lagern und Produktionsstätten eingesetzt werden (FTF, AMR)
- Schwere Nutzfahrzeuge
- Öffentlicher Verkehr (Busse, Oberleitungsbusse, Straßenbahnen)
- Schienenverkehr (Züge, Lokomotiven, Rangierlokomotiven)
- Ausrüstung für den Containerumschlag in Häfen (RTG-Kräne, Portalhubwagen, FTF)
- Flughafenausrüstung (GSE, Taxibot, Gepäckabfertigung)
- Lastkraftwagen und Bagger
- Technische Servicefahrzeuge (Müllwagen, Materialtransportfahrzeuge, Multitrucks)
- Schiffe (Fähren, Schlepper, Yachten)
- Bergbaufahrzeuge (Bohrer, Bagger, Schwerlastwagen)
- Militärische Hybridfahrzeuge mit leisem Betrieb
- Personenkraftwagen
Die gebräuchlichsten Arten von Lithiumbatterien für die Traktion
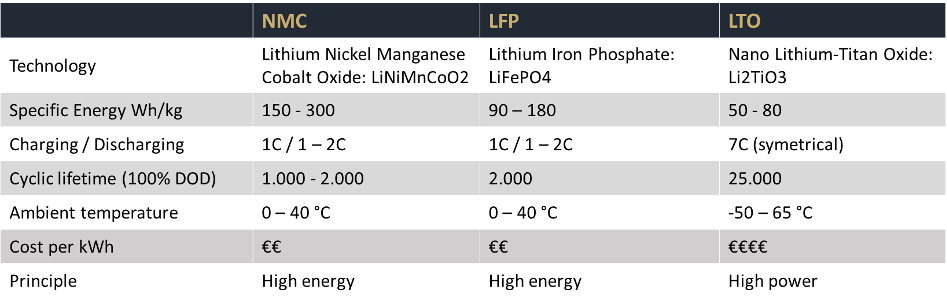
NMC | LFP | LTO | |
---|---|---|---|
Technologie | Lithium-Nickel-Mangan-Kobalt-Oxid: LiNiMnCoO2 | Lithium-Eisen-Phosphat: LiFePO4 | Nano-Lithium-Titan-Oxid: Li2TiO3 |
Spezifische Energie Wh/kg | 150 - 300 | 90 - 180 | 50 - 80 |
Aufladen/Entladen | 1C / 1 - 2C | 1C / 1 - 2C | 7C (symmetrisch) |
Zyklische Lebensdauer (100 % Entladetiefe) | 1.000 - 2.000 | 2.000 | 25.000 |
Umgebungstemperatur | 0 - 40 °C | 0 - 40 °C | -50 - 65 °C |
Kosten pro kWh | €€ | €€ | €€€€ |
Grundsatz | hohe Leistung | hohe Energie | hohe Leistung |
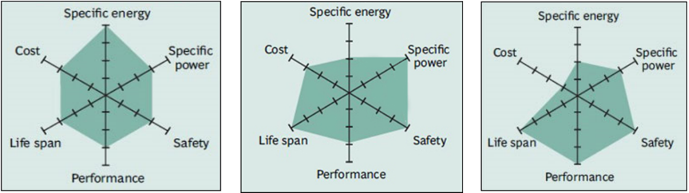
Specific energy | Spezifische Energie |
Cost | Kosten |
Life span | Lebensdauer |
Performance | Leistung |
Specific power | Spezifische Leistung |
Safety | Sicherheit |
Hauptparameter für die Auswahl der Batterietechnologie
- Erforderliche Lebensdauer
- Geschätzte Anzahl von Zyklen pro Tag/Jahr
- Maximal zulässiges Gewicht
- Erforderliche Leistung (Laden/Entladen) und Spannung
- Erforderliche Reichweite
- Lagerung (im Fahrzeug, auf dem Dach des Fahrzeugs)
- Erforderliche IP (Isolierung)
- Betriebsumgebungstemperatur
- TCO (Gesamtbetriebskosten) oder ROI (Return on Investment)
Für die Konzeption und Entwicklung eines Batteriesystems ist es unerlässlich, dass der in Frage kommende Batteriesystemintegrator über die Erfahrung oder die volle Unterstützung des Batteriezellen- und Modulherstellers verfügt.
Die folgenden Aufgaben fließen in die Entwicklung des Systems ein:
- Lebenszyklusanalyse auf der Grundlage des Energiebedarfs (Lastprofil)
- Thermische Analyse für die Auslegung des Kühlsystems und die Lagerung der Zellen/Module in der Box
- BMS-Design auf der Grundlage der Anzahl der Zellen in Reihe und der Anzahl der parallelen Zweige im System
- Auslegung der Batteriebox auf der Grundlage der erforderlichen Normen und Zulassungen (z. B. R10, R100, ISO 26262, SIL 0 – 3)
Die wichtigsten Funktionsprinzipien der heutigen Elektro- und Hybridfahrzeuge
- Langsames Aufladen, Aufladen über Nacht, Aufladen im Depot (Stunden)
- Lange Fahrten
- Geeignet für NMC, LFP
- Schnelles Aufladen, gelegentliches Aufladen, Aufladen während Stopps oder Stillstand (in der Größenordnung von 5 bis 20 Minuten)
- Betrieb 24 Stunden am Tag, 7 Tage die Woche
- Geeignet für LTO
- Hybridbatterie zum Ausgleich von Stromschwankungen und zur Rückgewinnung gespeicherter Energie
- Hybridbatterie für leisen und emissionsfreien Betrieb im gewünschten Bereich (5 bis 20 km)
Beispiel für den 24-Stunden-Betrieb
High energy batteries (NMC, LFP) | Hochenergiebatterien (NMC, LFP) |
SOC [%] | SOC [%] |
Time [hours] | Zeit [Stunden] |
SOC | Ladezustand |
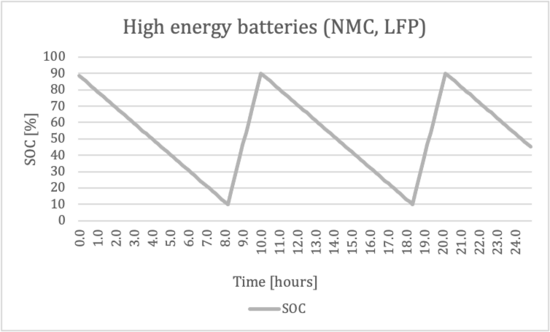
High power batteries (LTO) | Hochleistungsbatterien (LTO) |
SOC [%] | SOC [%] |
Time [hours] | Zeit [Stunden] |
SOC | Ladezustand |
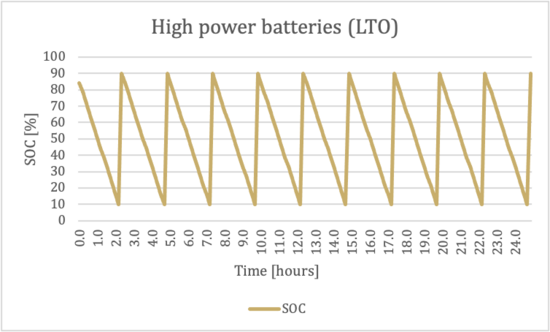
Schlussfolgerung
Ein Traktionsbatteriesystem kann für Fahrzeuge jeder Größe konzipiert werden. Von kleinen AMR-Robotern (0,5 kWh) über Busse und Züge (50 bis 600 kWh) bis hin zu Bergbaufahrzeugen (MWh).
[1] https://www.koridory.cz/e-407-001-prvni-elektricka-lokomotiva-csd-uvedena-do-provozu-1926/
https://cs.wikipedia.org/wiki/Lokomotiva_E_407.0
[2] https://batteryuniversity.com/article/bu-205-types-of-lithium-ion